This is an awful blaster that I just keep coming back to... I cherry-picked from 7 SSPB's and even picked darts that performed well and only got 12-18' stock with the best blaster. Good Lord! But it's fiddly. I like fiddly. It offers a challenge. So here's my answer. We'll do a hard tank expansion using a PVC end cap as a tank, a little ergo and a Nano Jolt integration for added rate of fire. Then for added rate of fire on the SSPB, some turrety goodness. The breech version uses no coupler and a CPVC end cap as a lower profile expansion. Nice but you'll want more!

Let's see what we'll need as far as materials :
1/2" schedule 40 PVC (scrap will do)
1/2" CPVC
1/2" PVC end cap (I'll show a substitute method that doesn't require this)
1/2" CPVC coupler
1/2" CPVC 90 degree elbow
Super glue & epoxy or PVC cement (thanks to torukmakto4 for the suggestions)
Here's the tools we'll be using :
Dremel w/various drum sanders
Hacksaw/coping saw
Small utility knife or X-acto
Small needle files - helpful
First let's start with some notes:
1) SSPB's will sometimes push darts out the front when pumping up. This is undesirable certainly. The pumps can feel off on some. Some have trouble pumping up, you need to take a few extra pumps at the beginning to seal the tank. I would avoid doing this mod on a really dodgy one. The tank expansion can cause fiddly ones to become even worse. Having said that, they sometimes smooth out as they wear in. I broke mine in a bit before cherry-picking. The 2 SSPB's we'll see here were the 2 worst ones I had NIB. One still had a little trouble sealing at first but is almost OK now, the other is now fine.
2) I foresee some questions about the durability of the tank expansion. I did an unintentional test with a 3 1/2' drop to a hard surface. It contacted to corner of the tank and there was no problem. I show a version with a CPVC end cap used as the tank expansion that is likely able to be run over with a car if you need to. The plastic in the area we'll be dealing with is quite thick.
3) Always keep your SSPB pumped up a bit while you are working on it. This will keep debris out of the tank. I add tape to the pump and blast button, shove a wet paper towel down the barrel and add a spitball to the valve area when exposed. You will empty the tank if you shove the spitball in too hard. Dust and debris are the enemy here. Be very mindful of this any time you are working on this blaster.
4) About the stock pump. It is possible to cut the pump housing cleanly (make a notch all of the way around with a thin ceramic sanding disc and X-acto the rest) and increase the efficiency by the usual teflon tape under the o-ring method. If your pump is faulty this is a good idea. If your pump works leave that for when it needs to be serviced. It's difficult to line up the pump properly after cutting it out, possibly negating the work. The gain in efficiency can be somewhat offset by the extra effort needed to push the tighter seal back. And plugging the pump isn't going to help much with ranges as there's already scary power to be unleashed. Having said that a plugged pump can give better performance with shotgun loads.
5) The Tek-3 spring makes a reasonable spring addition to the Jolt. It can feel crunchy. Some small length of the spring may need triming, bending and filing sharp edges.
6) You don't have to build it up using my methods if you know yours are going to be better obviously. What I show is what works at some level.
Let's start by building the extra tank. Hammer a small section of CPVC into a small piece of schedule 40 PVC as a test. If you find that there is just no way, sand down the inner surface of the PVC with a small, fine drum sanding attachment on your dremel (or a round needle file). Go very slowly since we want a hammer-in fit for strength. I hammered it in 1/8" carefully to insure straightness. Pull it back out and clean the surfaces involved well, preferably with alcohol. Apply your shoice of glue lightly to the sides of the last bit of the CPVC. Coat the face of the cut of the CPVC lightly as well for a chance at an internal superglue filet in one go. Hammer the PVC into the CPVC about 1/4" Let it dry in a warm place. I also added an additional fillet of superglue after it was dry.
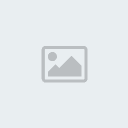
Next we'll cut the PVC off the CPVC section, leaving enough PVC to fit into our end cap at least 1/8". Cut the CPVC down to about 1". Make sure that the height of the tank will allow for the shell to slip under it. You can add a bit of volume by leaving your CPVC stub longer. I stupidly did not fit the stub to the side of the SSPB's tank before gluing. I would advise that you do that now. It's a few pics down. A large dremel drum sander is very close to the diameter of the SSPB's tank. Next, sand or file everything we cut to the point that nothing will ever fall into the tank. Nice and smooth.

Get the dust off everything as thoroughly as possible. If it's at all greasy or what-not clean it in the sink well. Double and triple check for particles anywhere inside the tank and inside the stub. Apply glue and set the stub into the end cap. I added an extra fillet of glue to the outside once that dried. A dart will keep out dust as we prepare the SSPB's tank.
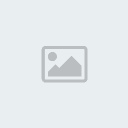
Wrap your SSPB's main body well with masking tape so no dust will get into anything. I sand down an area on the side of the SSPB's tank in the pictured location until it is paper thin in a circular area. Again using the small fine dremel attachment. Scuff up the plastic where the stub will meet the tank with 120 grit. Clean off any dust and hit the blast button to depressurize the tank. Cut away the circle with a very sharp small utility knife or an X-acto. I held it upside-down to trim any excess plastic and was careful to control where any plastic chips went. If you get some chips in the tank, computer duster or an air compressor are your best bet. Next best is probably washing it with water and letting it dry thoroughly. I have never tried that and wouldn't do it myself. Note that you can fiddle with the actual position of the hole a bit. Put it high up for a minute while we prep to attach the new tank.

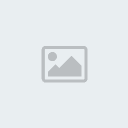
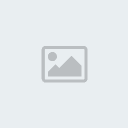
Now we'll glue the stub to the SSPB. Quadruple check the inside of the expansion tank for debris. Apply super glue to the face of the CPVC stub (add a fillet of glue to the outside later as usual) and carefully lower & center it over the hole aligning it nice and perpendicular like so :
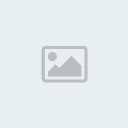
After that's dry (1-min epoxy users are laughing) we can work on adding a CPVC coupler. Here's how I score and cut the barrel away from the barrel support with a utility knife (mostly just in case) :

Here's the cut at the barrel end (saw through that very tightly packed moist towel). Now a note on the breech SSPB shown at the start. The barrel stub left (on the SSPB) is a nice match to the I.D. of schedule 40 1/2" PVC (which makes a nice breech). You can glue a breech right to this stub. Better rate of fire than stock and slightly more accurate than the turreted version. Unconventional but doable. There's not alot of room for a PVC coupler if you want to retain the shells but it might work.

Here's the barrel stub I left. It's surely possible to remove more for less deadspace but this is nice and sturdy. Note the spitball. Also note that the half-coupler I show has had the inside edge the barrel would normally stop on, sanded away for less deadspace. Trim down the barrel support for the coupler.

Smooth and fit everything carefully. I use a good length of barrel to check the alignment of everything. Get it all dust free & clean as usual. Glue on your coupler with epoxy or PVC cement. You can use super glue if you are very careful. Be generous enough to create a filet of glue on the face but not enough to pool away and get near the valve. Add a filet to the outside after it's dry. Let it dry in a nice warm spot, undisturbed, till it cures.
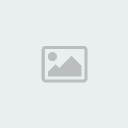
Now we can rape the shell. Just slightly. I made my slot for the CPVC stub a bit too long (far back). Fitting the shell involves sliding the shell, level with the blaster, along that slot and around the stub of the tank. This can be fiddly and needs to be right or you'll be hearing things you don't want to hear. Just go along noting where the shell interferes, back the shell off the stub and trim as needed. Some trimming of the internal brace midway through the shell is needed. Note that the screw bosses, although trimmed slightly are sturdy. You can see that I trimmed the sharp front edge of the shell here to allow the turret to sit a little farther back (thus reducing that dreaded deadspace). The top of the coupler needs to be rounded just slightly

Next let's make a Jolt integration easy. Sand down the puny pump handle until you remove the ridges and flatten the dome at the front. Test fit a 90 degree CPVC elbow over the trimmed pump handle. Try to insure that it lines up nice and parallel to the barrel and sinks in as much as possible to protect the guts of the pump. I wrap the SSPB up in the tail of my t-shirt so I don't have to do any fiddly taping to keep dust out of the pump. Cut a little length of CPVC and use a scrap piece of coupler for the pump handle bottom. Round this over to remove any sharp edges.
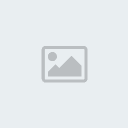
This will go together like so:

Here's a different setup with a 6" barrel that gets excellent ranges (even with stock darts).

A final bit of ergo on the back of the shell. I rounded the back up just a bit as there's not much plastic here.

Now we'll formally introduce SSPB to Jolt. Take a small length of CPVC and shape it to the overall profile of the Jolt's grip. Sand the paint off of the grip area of the Jolt as well. Line it up carefully as the fit determines how the Jolt aims up and down. You can strategically add a drop of super glue on the CPVC stub if it winds up crooked. Just to add material and cock it in the coupler the way you want. After fitting, glue with epoxy and try to add some clamping force as it dries. We can trim down the CPVC once we try it out for interference with the right hand.

Here it is with a turreted Nano. I trimmed down the priming rod a bit so it didn't hit my finger when fired.
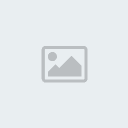
High and low profile Jolt integrations. The wrist-strap really helps and I would recommend trying it out.

Note the difference in the height and attachment points of the CPVC stub.

Finally here is a tank made from a 1/2" PVC coupler, PVC & CPVC nested as usual and a crayon end used as the end of the tank. Just in case you are short an end cap. Or want even more volume. Muwahahaha!
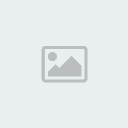

The SSPB performs very well with the added volume. I should mention that I rapid-fire pumped the SSPB's by feel not number. It takes me 2 seconds at best to pump and fire one shot at the pressure that tested out to 12 good pumps. It seems to work out to 9-10 super quick pumps. The oprv kicks in at 22 pumps. As few as 7 good pumps gets you in the 35' range with a 2 3/4" barrel and stock darts. I hit my neighbors shutters across the way with stefans, a 6" barrel and 22 good pumps. That's 118' from the muzzle, flat at shoulder height. The 4 1/8" barrels on the turret hit 90'+ with stefans at 12 pumps, and 100+ with a full tank. With whistlers and taggers the turret gets 65' at 12 pumps. I haven't found the optimal single-barrel length for stock darts yet. Short barrels, lots of pumps and stock darts don't mix well here. It'll just shred the dart. The turrets' barrels were sized with rate of fire in mind. Shorter barrels, fewer pumps to get good ranges. The tank expansion was sized with rate of fire in mind as well. A quick way to load stefans to the back of the SSPB's barrels is to push the darts in and blow down the end of each barrel, spinning the turret to clear the air holes at the back. Weird, I know. The Jolt has a stock spring (I will build a 2.5" turret w/an Ultimate Berserker spring) and gets 55'. In usage when integrated the left hand can cradle & fire the Jolt, advance the turrets & pump the SSPB up. The right can prime the Jolt and fire the SSPB. Or you can switch the SSPB and Jolt into the right hand to fire either as needed. The end cap winds up making a nice thumb-rest, giving you a slightly surer grip and better aim. The wrist strap is Excellent! It makes priming a snap even with heavy springs. I use a Wii-mote one, which can clamp pretty securely onto the wrist. Working time without curing time on this one is about 2 hours without the turret.

Let's see what we'll need as far as materials :
1/2" schedule 40 PVC (scrap will do)
1/2" CPVC
1/2" PVC end cap (I'll show a substitute method that doesn't require this)
1/2" CPVC coupler
1/2" CPVC 90 degree elbow
Super glue & epoxy or PVC cement (thanks to torukmakto4 for the suggestions)
Here's the tools we'll be using :
Dremel w/various drum sanders
Hacksaw/coping saw
Small utility knife or X-acto
Small needle files - helpful
First let's start with some notes:
1) SSPB's will sometimes push darts out the front when pumping up. This is undesirable certainly. The pumps can feel off on some. Some have trouble pumping up, you need to take a few extra pumps at the beginning to seal the tank. I would avoid doing this mod on a really dodgy one. The tank expansion can cause fiddly ones to become even worse. Having said that, they sometimes smooth out as they wear in. I broke mine in a bit before cherry-picking. The 2 SSPB's we'll see here were the 2 worst ones I had NIB. One still had a little trouble sealing at first but is almost OK now, the other is now fine.
2) I foresee some questions about the durability of the tank expansion. I did an unintentional test with a 3 1/2' drop to a hard surface. It contacted to corner of the tank and there was no problem. I show a version with a CPVC end cap used as the tank expansion that is likely able to be run over with a car if you need to. The plastic in the area we'll be dealing with is quite thick.
3) Always keep your SSPB pumped up a bit while you are working on it. This will keep debris out of the tank. I add tape to the pump and blast button, shove a wet paper towel down the barrel and add a spitball to the valve area when exposed. You will empty the tank if you shove the spitball in too hard. Dust and debris are the enemy here. Be very mindful of this any time you are working on this blaster.
4) About the stock pump. It is possible to cut the pump housing cleanly (make a notch all of the way around with a thin ceramic sanding disc and X-acto the rest) and increase the efficiency by the usual teflon tape under the o-ring method. If your pump is faulty this is a good idea. If your pump works leave that for when it needs to be serviced. It's difficult to line up the pump properly after cutting it out, possibly negating the work. The gain in efficiency can be somewhat offset by the extra effort needed to push the tighter seal back. And plugging the pump isn't going to help much with ranges as there's already scary power to be unleashed. Having said that a plugged pump can give better performance with shotgun loads.
5) The Tek-3 spring makes a reasonable spring addition to the Jolt. It can feel crunchy. Some small length of the spring may need triming, bending and filing sharp edges.
6) You don't have to build it up using my methods if you know yours are going to be better obviously. What I show is what works at some level.
Let's start by building the extra tank. Hammer a small section of CPVC into a small piece of schedule 40 PVC as a test. If you find that there is just no way, sand down the inner surface of the PVC with a small, fine drum sanding attachment on your dremel (or a round needle file). Go very slowly since we want a hammer-in fit for strength. I hammered it in 1/8" carefully to insure straightness. Pull it back out and clean the surfaces involved well, preferably with alcohol. Apply your shoice of glue lightly to the sides of the last bit of the CPVC. Coat the face of the cut of the CPVC lightly as well for a chance at an internal superglue filet in one go. Hammer the PVC into the CPVC about 1/4" Let it dry in a warm place. I also added an additional fillet of superglue after it was dry.
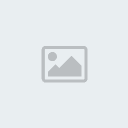
Next we'll cut the PVC off the CPVC section, leaving enough PVC to fit into our end cap at least 1/8". Cut the CPVC down to about 1". Make sure that the height of the tank will allow for the shell to slip under it. You can add a bit of volume by leaving your CPVC stub longer. I stupidly did not fit the stub to the side of the SSPB's tank before gluing. I would advise that you do that now. It's a few pics down. A large dremel drum sander is very close to the diameter of the SSPB's tank. Next, sand or file everything we cut to the point that nothing will ever fall into the tank. Nice and smooth.

Get the dust off everything as thoroughly as possible. If it's at all greasy or what-not clean it in the sink well. Double and triple check for particles anywhere inside the tank and inside the stub. Apply glue and set the stub into the end cap. I added an extra fillet of glue to the outside once that dried. A dart will keep out dust as we prepare the SSPB's tank.
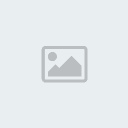
Wrap your SSPB's main body well with masking tape so no dust will get into anything. I sand down an area on the side of the SSPB's tank in the pictured location until it is paper thin in a circular area. Again using the small fine dremel attachment. Scuff up the plastic where the stub will meet the tank with 120 grit. Clean off any dust and hit the blast button to depressurize the tank. Cut away the circle with a very sharp small utility knife or an X-acto. I held it upside-down to trim any excess plastic and was careful to control where any plastic chips went. If you get some chips in the tank, computer duster or an air compressor are your best bet. Next best is probably washing it with water and letting it dry thoroughly. I have never tried that and wouldn't do it myself. Note that you can fiddle with the actual position of the hole a bit. Put it high up for a minute while we prep to attach the new tank.

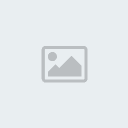
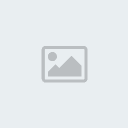
Now we'll glue the stub to the SSPB. Quadruple check the inside of the expansion tank for debris. Apply super glue to the face of the CPVC stub (add a fillet of glue to the outside later as usual) and carefully lower & center it over the hole aligning it nice and perpendicular like so :
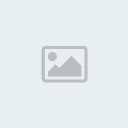
After that's dry (1-min epoxy users are laughing) we can work on adding a CPVC coupler. Here's how I score and cut the barrel away from the barrel support with a utility knife (mostly just in case) :

Here's the cut at the barrel end (saw through that very tightly packed moist towel). Now a note on the breech SSPB shown at the start. The barrel stub left (on the SSPB) is a nice match to the I.D. of schedule 40 1/2" PVC (which makes a nice breech). You can glue a breech right to this stub. Better rate of fire than stock and slightly more accurate than the turreted version. Unconventional but doable. There's not alot of room for a PVC coupler if you want to retain the shells but it might work.

Here's the barrel stub I left. It's surely possible to remove more for less deadspace but this is nice and sturdy. Note the spitball. Also note that the half-coupler I show has had the inside edge the barrel would normally stop on, sanded away for less deadspace. Trim down the barrel support for the coupler.

Smooth and fit everything carefully. I use a good length of barrel to check the alignment of everything. Get it all dust free & clean as usual. Glue on your coupler with epoxy or PVC cement. You can use super glue if you are very careful. Be generous enough to create a filet of glue on the face but not enough to pool away and get near the valve. Add a filet to the outside after it's dry. Let it dry in a nice warm spot, undisturbed, till it cures.
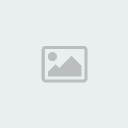
Now we can rape the shell. Just slightly. I made my slot for the CPVC stub a bit too long (far back). Fitting the shell involves sliding the shell, level with the blaster, along that slot and around the stub of the tank. This can be fiddly and needs to be right or you'll be hearing things you don't want to hear. Just go along noting where the shell interferes, back the shell off the stub and trim as needed. Some trimming of the internal brace midway through the shell is needed. Note that the screw bosses, although trimmed slightly are sturdy. You can see that I trimmed the sharp front edge of the shell here to allow the turret to sit a little farther back (thus reducing that dreaded deadspace). The top of the coupler needs to be rounded just slightly

Next let's make a Jolt integration easy. Sand down the puny pump handle until you remove the ridges and flatten the dome at the front. Test fit a 90 degree CPVC elbow over the trimmed pump handle. Try to insure that it lines up nice and parallel to the barrel and sinks in as much as possible to protect the guts of the pump. I wrap the SSPB up in the tail of my t-shirt so I don't have to do any fiddly taping to keep dust out of the pump. Cut a little length of CPVC and use a scrap piece of coupler for the pump handle bottom. Round this over to remove any sharp edges.
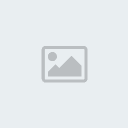
This will go together like so:

Here's a different setup with a 6" barrel that gets excellent ranges (even with stock darts).

A final bit of ergo on the back of the shell. I rounded the back up just a bit as there's not much plastic here.

Now we'll formally introduce SSPB to Jolt. Take a small length of CPVC and shape it to the overall profile of the Jolt's grip. Sand the paint off of the grip area of the Jolt as well. Line it up carefully as the fit determines how the Jolt aims up and down. You can strategically add a drop of super glue on the CPVC stub if it winds up crooked. Just to add material and cock it in the coupler the way you want. After fitting, glue with epoxy and try to add some clamping force as it dries. We can trim down the CPVC once we try it out for interference with the right hand.

Here it is with a turreted Nano. I trimmed down the priming rod a bit so it didn't hit my finger when fired.
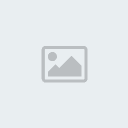
High and low profile Jolt integrations. The wrist-strap really helps and I would recommend trying it out.

Note the difference in the height and attachment points of the CPVC stub.

Finally here is a tank made from a 1/2" PVC coupler, PVC & CPVC nested as usual and a crayon end used as the end of the tank. Just in case you are short an end cap. Or want even more volume. Muwahahaha!
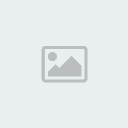

The SSPB performs very well with the added volume. I should mention that I rapid-fire pumped the SSPB's by feel not number. It takes me 2 seconds at best to pump and fire one shot at the pressure that tested out to 12 good pumps. It seems to work out to 9-10 super quick pumps. The oprv kicks in at 22 pumps. As few as 7 good pumps gets you in the 35' range with a 2 3/4" barrel and stock darts. I hit my neighbors shutters across the way with stefans, a 6" barrel and 22 good pumps. That's 118' from the muzzle, flat at shoulder height. The 4 1/8" barrels on the turret hit 90'+ with stefans at 12 pumps, and 100+ with a full tank. With whistlers and taggers the turret gets 65' at 12 pumps. I haven't found the optimal single-barrel length for stock darts yet. Short barrels, lots of pumps and stock darts don't mix well here. It'll just shred the dart. The turrets' barrels were sized with rate of fire in mind. Shorter barrels, fewer pumps to get good ranges. The tank expansion was sized with rate of fire in mind as well. A quick way to load stefans to the back of the SSPB's barrels is to push the darts in and blow down the end of each barrel, spinning the turret to clear the air holes at the back. Weird, I know. The Jolt has a stock spring (I will build a 2.5" turret w/an Ultimate Berserker spring) and gets 55'. In usage when integrated the left hand can cradle & fire the Jolt, advance the turrets & pump the SSPB up. The right can prime the Jolt and fire the SSPB. Or you can switch the SSPB and Jolt into the right hand to fire either as needed. The end cap winds up making a nice thumb-rest, giving you a slightly surer grip and better aim. The wrist strap is Excellent! It makes priming a snap even with heavy springs. I use a Wii-mote one, which can clamp pretty securely onto the wrist. Working time without curing time on this one is about 2 hours without the turret.
Last edited by iamthatcat on Tue Feb 07, 2012 7:11 am; edited 5 times in total